The HLTNC 80 AST 750W 2.4N 1KW 3.8N 220V AC Servo Motor Kit is designed for CNC engraving machines. It includes a magnetic 17-bit absolute encoder and T3D 20A driver for precise control and high performance. This kit provides reliable and efficient operation for engraving applications. It is capable of handling heavy workloads and delivering smooth and accurate movements. The servo motor kit offers a powerful and durable solution for CNC engraving projects.
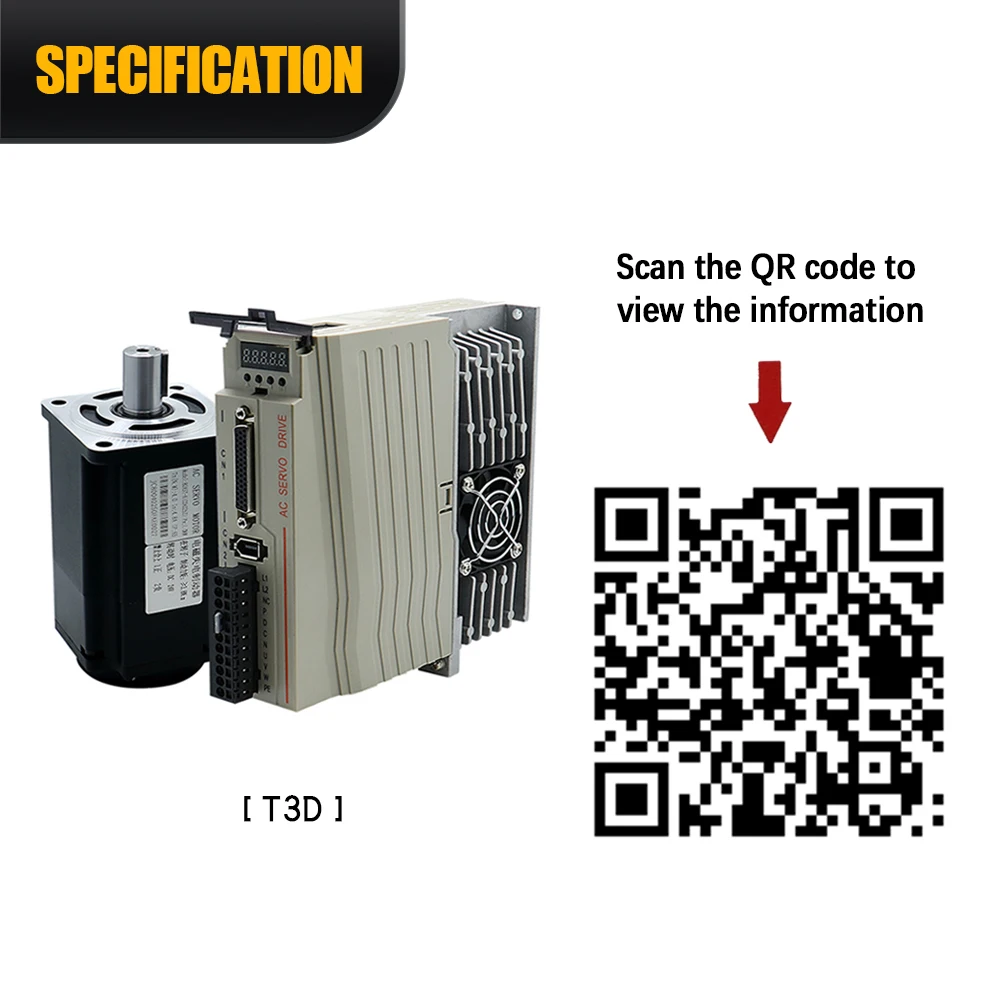
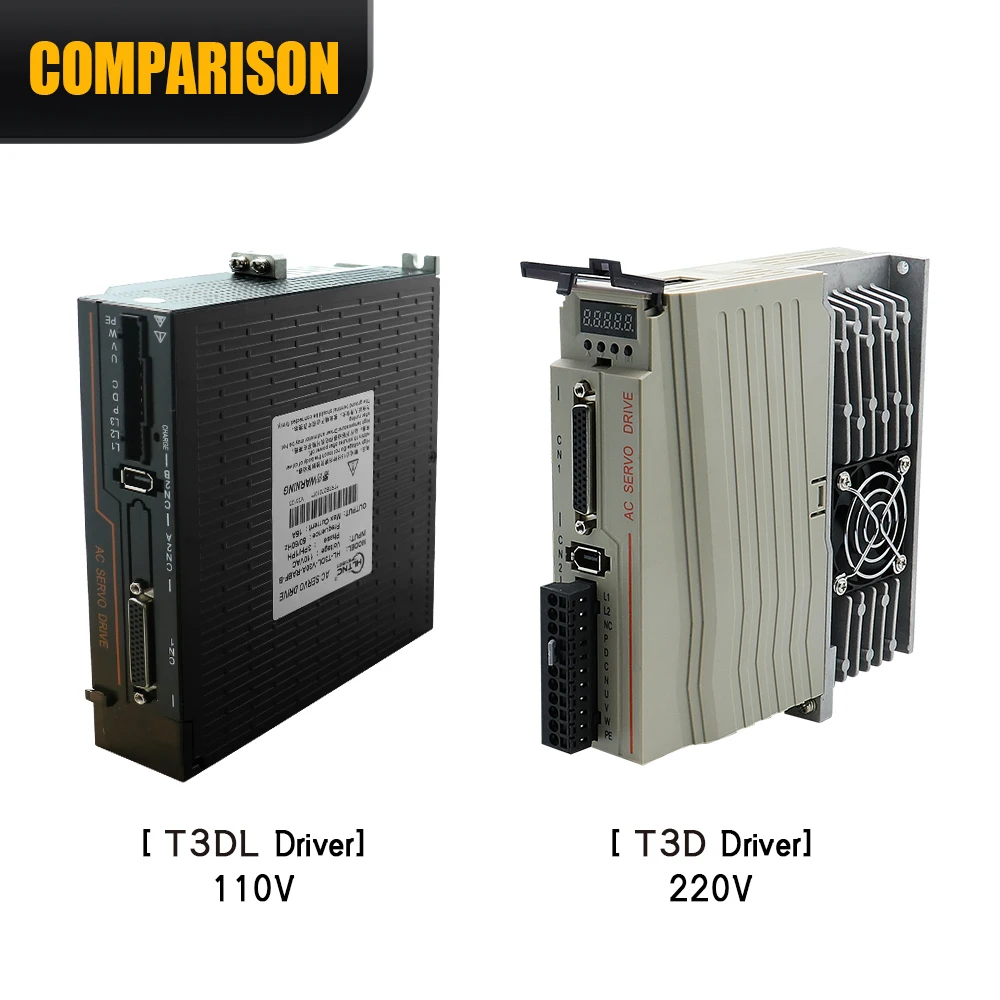
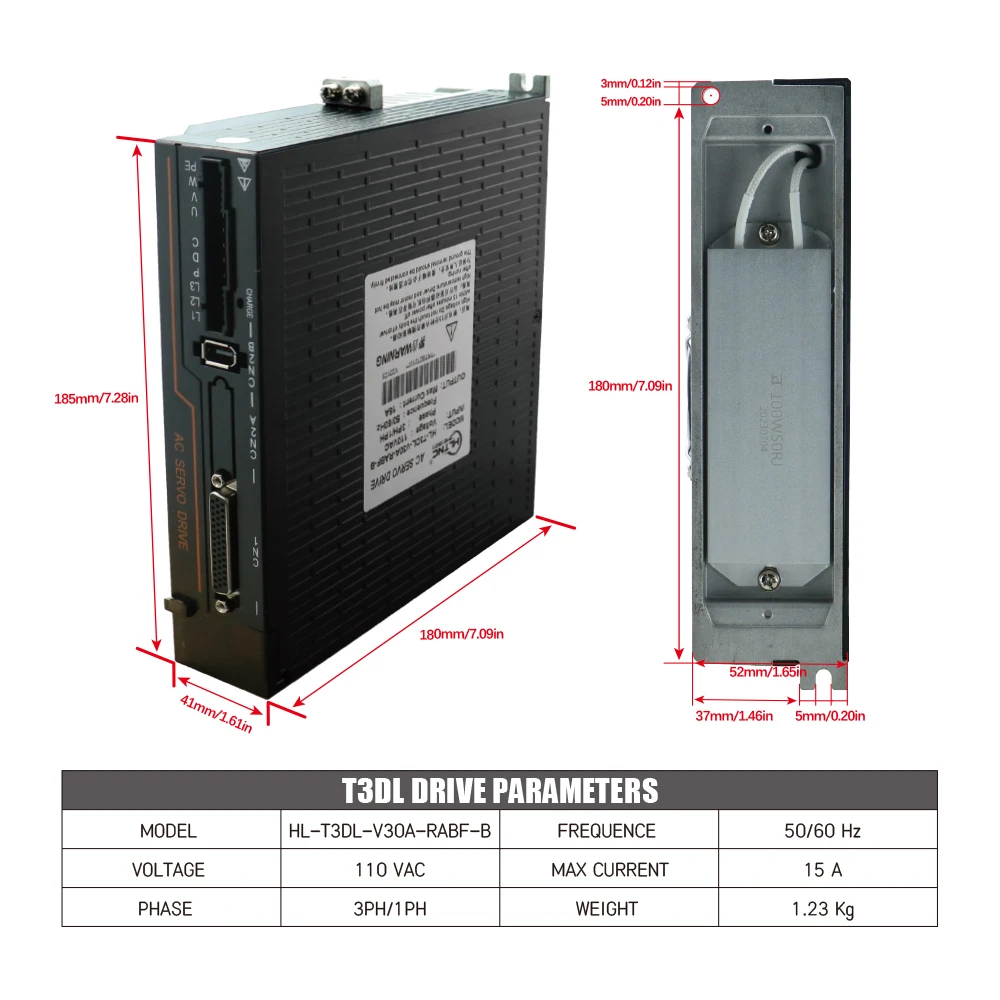
Servo Motor With Magnetic 17bit Absolute Encoder
|
||||||
Servo Motor Model |
Motor Flange |
Power |
RS485 (Modbus) |
Customized cable length |
Brake |
Motor Shaft Diameter |
Nema24 60mmx60mm (mounting hole distance 49.5mm) |
400w |
Support |
Support (3-15meter) |
Optional |
14mm With 5mm Key |
|
600w |
||||||
Nema32 80mmx80mm ( mounting hole distance 63.6mm ) |
750w |
19mm With 6mm Key |
||||
1000w |
Simple user manual , please download it from the link below.
for more information, please contact with us.
3D file for the motor could be provide
Main control signal |
Pulse(5v or 24v Pulse signal); analog voltage (0-10v); modbus RS485 |
Support System |
CNC, PLC Controller |
24V Pulse Signal |
P+ and D+ port connected with 2K 1/4W resistor, or the driver would be damaged |
Motor With Brake |
the brake should be connected with 24v DC power supply and relay (see diagram below) |
Main setting |
P-036 shaft rotate direction (1: reverse and 0:forward) P-098 (1:internal enable sigal and 0:external enable siganl) P-029 electric gea ratio (larger value,higer speed) long press E-SEF to show DONE,save parameter setting sucessfully, then restart the driver |

Option 1: |
||||
|
||||
|
1* 750W 80AST-A1C02430 Servo Motor ( 17 bit absolute ) |
|||
|
1* T3D-L20A AC Driver |
|
1* 3Meter Encoder Cable + Power Cable |
|
|
1* Control Signal Cable |
|
2* 2K 1/4W resistance |
|
Option 2: |
||||
|
||||
|
1* 1KW 80AST-A1C04025 Servo Motor ( 17 bit absolute ) |
|||
|
1* T3D-L20A AC Driver |
|
1* 3Meter Encoder Cable + Power Cable |
|
|
1* Control Signal Cable |
|
2* 2K 1/4W resistance |
|
if you need PDF manual and software of the driver, please contact with us

|
1. Stable performance and fast response |
|
2.Advanced heat dissipation design process |
|
3.Applicable to various automation equipment |
Technical Specifications |
||||
Rated Voltage ( V) |
220 |
220 |
220 |
220 |
Rated Power ( W) |
400 |
600 |
750 |
1000 |
Rotor pole pairs ( P ) |
5 |
5 |
5 |
5 |
Rated Torque ( Nm ) |
1.27 |
1.91 |
2.4 |
3.8 |
Instantaneous max torque (Nm ) |
3.82 |
5.73 |
7.2 |
11.4 |
Rated Speed / Max Speed (rpm) |
3000/6000 |
3000/6000 |
3000/5000 |
2500/3000 |
Rated Current ( A ) |
2.8±10% |
4±10% |
4.8±10% |
|
Instantaneous Max Current (A ) |
8.4±10% |
12±10% |
14.4±10% |
|
Moment Coefficient (Nm/A ) |
0.42±10% |
0.54±10% |
0.5±10% |
0.93±10% |
Back EMF Coefficient ( X10 V/rpm) |
27.5±10% |
32.5±% |
33.2±10% |
56±10% |
Resistance (Ω ) |
3±10% ( 20℃ ) |
3.2± 10%(20 ℃) |
1.6 ± 10%(20 ℃) |
3±10%(20℃) |
Inductance ( mH) |
7.8±20% ( 20℃ ) |
8.4±20% ( 20℃) |
9.5±20% (20℃) |
19±20% (20℃) |
Moment of inertia ( X10V/rpm ) |
0.68 [0.73] ± 10% |
0.82[1.7] ± 10% |
1.72 [1.77]± 10% |
2.4[2.45]±10% |
Max radial load ( N ) |
245 |
392 |
||
Max axial load ( N ) |
74 |
147 |
||
Weight ( KG) |
1.22 [1.65]± 10% |
1.4[1.7]±10% |
2.2[3]±10% |
2.71[3.36]±10% |
Encoder Resolution |
10000ppr |
|||
Protection Structure |
IP65 |
|||
Insulation class |
F |
|||
Insulation Resistance |
More than 20m Ω DC500V |
|||
Insulation Withstand voltage |
AC 1500V 1minutes |
|||
Vibration Level |
Rated A for operation |
|||
Turn Around |
Forward turn command,viewed from load sid, counterclockwise (CCW) |
|||
Surroundings |
Temperature -20℃ ~ 40 ℃, humidity 20% ~ 80% RH ( no condensation ) , altitude below 1000 |
|||
Temperature – 20℃ ~ 60℃, (no freezing) humidity 20% ~ 80% RH (no condensation) |
||||
Impact Strength |
98m/S ² |
|||
Vibration Resistance |
49m/S ² |
Power |
400w |
600w |
750w |
1000w |
Rated Voltage DC (V) |
24±10% |
|||
Rated Power (W) |
0.3 |
0.56 |
||
Insulation Class |
F |
|||
Static Torque (Nm) |
≥1.5 |
≥2 |
≥4 |
|
Insulation Resistance (MΩ ) |
>500 |
|||
Resistant to high voltage |
1500V/1S/5mA |
|||
Rotary Clearance |
≤0.5 |
|||
Operating Ambient Temperature |
-10~+40 |
|||
Attract Time |
≤50 |
≤60 |
||
Release Time |
≤20 |
|||
Attract Voltage |
≤19.2 |
|||
The release of the voltage |
>1.5 |
|||
Running noise |
<60 |
Symbol |
Name |
Function |
POW |
Power Light (none) |
The decimal point of the second digital bube from the left lights up to indicate that the servo is under voltage |
RUN |
Runing light (none) |
The decinal point of the first digital tube from the left lights up to indicate that the servo is enabled |
▲ |
Add key |
Increase the serial number of value, long press has repeat effect |
▼ |
Decrease Key |
Decrease the serial number of value,long preass haas repeat effect |
◀ |
Exit Key |
Menu exit, operation cancelled, |
SET |
Enter |
Menu Entry,parameter modification confirmation or operation confirmation |
Set After Power on:
Find P-098 and change it to 1
Find the E-SEF, press and hold the confirmation key until it shows DONE. then the parameters has been saved successfully. After all parameters are set, power off and restart.
Common parameters:
P-036 is changed to 1 (reverse direction) 0 (positive direction) motor direction conversion parameter. The default is 1 reverse direction
P-029 (electronic gear ratio numerator) is 1 by default, the higher the value, the faster the speed
(The above parameters are general setting parameters. If you need to modify other parameters, please refer to the manual or contact the technical/sales personnel)
The following parameters are rigid adjustment parameters. No adjustment is needed if the equipment is OK
P-005 (Speed ring rigidity)
P-009 (Position ring rigidity)
P-006 (generally, the maximum setting is about 100)
P-019 (generally, the maximum setting is about 300)
The specific adjustment of rigid parameters depends on the transmission structure and load of the equipment. Contact the after-sales service personnel for specific questions.
Reviews
There are no reviews yet.